Timing Chart
Here, I/O timings of various commands are described.
When "Output Control" Is Set to "None"
Output the measurement results if controller is not synchronous with external devices. Have the external devices detect the GATE signal of the controller, and load measurement results during ON status.
Inputting a measurement trigger in the STEP signal
Example) When 3 expressions are set in [Parallel Data Output]:
Output signal
| |
---|
| Turns on when the controller is available for measurement and the RUN window is displayed. It is OFF in the ADJUST window, so switch to the RUN window during operation. |
| Indicates that controller is currently measuring or switching the scene. Do not input next command while the BUSY signal is on. Otherwise, on-going processing or commands that are input will not be performed correctly. |
| |
| Outputs the results for expressions set in the processing item [Parallel Judgement Output]/[Parallel Data Output]. |
| Used to control the loading time of measurement results to external devices. ON for the time required for external devices to securely load measurement results. Set the output cycle so that the total output time is shorter than measurement interval (input interval of STEP signal). The GATE signal can be output only after the [Parallel Judgement Output] and [Parallel Data Output] are set in the measurement flow. |
| ON when STEP signal can be input. When through images are being displayed, the READY signal will turn to OFF, but the STEP signal is received. |
Input signal
| |
---|
| Input measurement triggers from external devices such as optic switches, etc. Perform measurement once synchronous with the STEP signal turning on (OFF →ON). Turn the STEP signal ON for at least 0.5 ms. A noise filter (filter initial setting value: 100 μs) is set in STEP input. |
Reference- The following can be changed with regard to the READY signal.
- Handling of ERROR signal when STEP signal is input during measurement
Important
- When parallel continuous measurement is engaged and continuous STEP signal is input, switching of scene group should be avoided. When this is performed, set "Unchecked" in "Save scene group on switch scene" in either of the settings items below.
Continuous measurement
Important
- Measurement is given priority when continuous measurement is being performed. As a result, the measurement result display (overall judgement, image, judgement for each processing unit in the flow display, detailed results) may not be updated.
When continuous measurement ends, the measurement results of the final measurement are displayed.
Example) When 1 expressions are set in [Parallel Data Output]:
ReferenceInput signal
| |
---|
| |
| This is the execution trigger. After DI0 to 6 is set, turn DI7 on after an interval over 1 ms. |
Reference- The ERROR signal turns on when the input command is not correctly performed.
When "Output Control" Is Set to "Handshaking"
Output the measurement results if controller is synchronous with external devices. If this function is used when multiple measurement results are output in sequence, it enables efficient and effective data transfer.
Inputting a measurement trigger in the STEP signal
Example) When 3 expressions are set in [Parallel Data Output]:
ReferenceInput signal
| |
---|
| This signal is used to request the next data transfer from external devices. The controller does not output data until the DSA signal is on. Turn the DSA signal on in the following cases: - The receiving system for external devices is complete
- The controller has completed measurement
The BUSY signal is on during measurement. As a result, the timing of when measurement is complete can be understood by observing the BUSY signal. |
When "Output Control" Is Set to "Synchronization Output"
This method enables synchronization between processing timing on the line and timing for output of controller results. After the STEP signal has turned on the number of times set in "number of delay" in the communication specifications, measurement results will be output the next time the STEP signal turns on.
Reference- When the communication specification "Output Control" is set to "Synchronization output", levels will be counted according to the number of times the STEP signal turns on. For this reason, perform settings so that results are output only once for each measurement. (1 unit for [Judgement Output], 1 data item for [Data Output])
Setting Communication Specifications (Parallel Interface) - Only designate the STEP signal for measurement command input.
When measurement using serial commands and continuous measurement are performed, the output time will not match and this can cause controller malfunctions.
Example) Stepped transmission line utilizing star wheel
The discharge timing for when a defective part is found and the measurement results output timing can be synchronized.
Inputting a measurement trigger in the STEP signal
Example) When "2" is set for "Number of delay"
ReferenceScene/Scene Group Switch
Output signal
| |
---|
| Turns on when the controller is available for measurement and the RUN window is displayed. Turns off in the ADJUST window. |
| Indicates that the controller is currently switching the scene or scene group. Do not input next command while the BUSY signal is on. Otherwise, on-going processing or commands that are input will not be performed correctly. |
Input signal Scene switching
| |
---|
| |
| |
| |
| This is the execution trigger. After DI0 to 6 is set, turn DI7 on after an interval over 1 ms. BUSY signal is on during implementation of commands. After checking that the BUSY signal has turned on, turn DI7 off, and then turn DI0 to 6 off. |
Input signal Scene group switching
| |
---|
| Set scene group No. (0 to 31). |
| |
| |
| This is the execution trigger. After DI0 to 6 is set, turn DI7 on after an interval over 1 ms. BUSY signal is on during implementation of commands. After checking that the BUSY signal has turned on, turn DI7 off, and then turn DI0 to 6 off. |
About Multiple Image Input Function
The function that enables continuous high speed image input is called the multiple image input function. The next STEP signal can be received at the point when image input is complete. It is not necessary to wait until measurement processing is complete. Whether image input is complete or not can be checked with the status of the READY signal.
In the case of FZ3-9


/H9


where two CPUs are installed, you can use the [Single-line High-speed mode] function that causes the two CPUs to alternately process measurement to shorten the shortest takt time
*1 to as much as one half.
*1: The shortest takt time refers to the shortest time over which a STEP can be accepted without generating a pool of captured images.
Important
- Set the image mode to "Freeze".
- When loading images continuously at high speed, the number of images that can be loaded is limited. Once the maximum number of images have been loaded, the READY signal will not turn on until the current measurement processing is complete. Accordingly, the next STEP cannot be input.
About Max. Number of Loading Images during Multiple Image Input - If STEP is input while READY is off, the ERROR terminal turns on.
- Even if the image mode is "Through", the multiple image input function can be used. Note, however, that the READY signal is always off at this time and whether image input is complete cannot be observed from the outside. Even if the READY signal remains off, STEP signals can be accepted without the ERROR terminal turning on. Therefore, at this time, make the STEP signal input interval slightly longer than the image input time.
- If triggers are input continuously and too quickly for the communication output to catch up, some steps may not be output or measurement delays may occur. Input triggers at appropriate timings that do not cause communication delays.
- The multiple image input function cannot be used in the following cases:
- Multiple camera input processing units are present in the flow.
- An HDR+ camera is present in the flow.
- 1 camera input processing unit is used in multiple processes using the branching function.
- Measurement triggers are input other than in the parallel mode (such as when non-procedure commands or PLC-link measurement commands are sent).
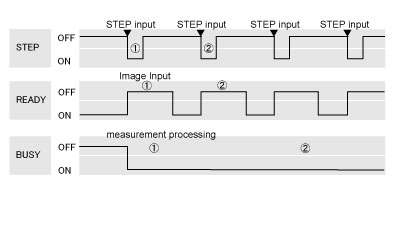
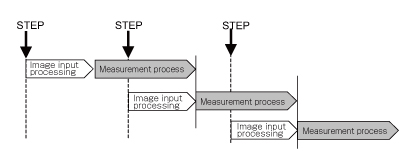